A Detailed Review of Container Welding Examination Specifications and Methodologies for Improved Weld Quality and Efficiency
The relevance of welding evaluation standards in the production of storage tanks can not be overstated, as they serve as the backbone for guaranteeing weld stability and operational dependability. Different examination strategies, consisting of aesthetic evaluations and advanced non-destructive screening approaches, are important in determining potential problems that can compromise efficiency.
Value of Welding Examination Specifications
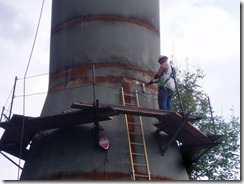
Welding inspection requirements encompass a variety of criteria, including product specs, welding procedures, and certifications of employees associated with the welding process. By enforcing these standards, companies can methodically identify and remedy prospective defects, consequently reducing the possibility of pricey repair services or devastating failures. Moreover, extensive assessment methods foster a culture of responsibility and accuracy, urging welders to keep high levels of craftsmanship.
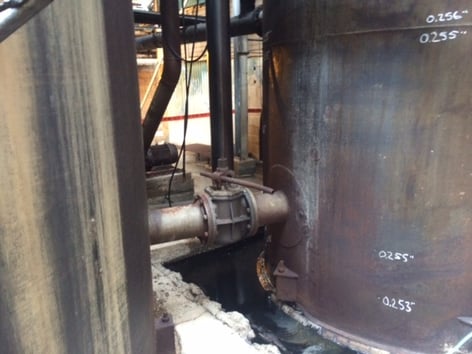
Typical Welding Assessment Methods


Ultrasonic Examining (UT) is an additional prevalent technique, making use of high-frequency acoustic waves to spot inner flaws that might not show up on the surface. This approach is especially efficient for recognizing gaps or inclusions within the weld metal. Magnetic Fragment Evaluating (MT) is also commonly utilized, particularly for ferromagnetic products, as it reveals surface and near-surface issues with the application of magnetic fields and ferrous particles.
Additionally, Liquid Penetrant Screening (PT) finds surface-breaking problems by applying a penetrant to the weld and then using a programmer to extract the penetrant. Each of these methods adds to a comprehensive assessment approach, guaranteeing that welds meet the rigid quality requirements required in tank construction.
Regulatory Requirements and Conformity
Regulative requirements and compliance are crucial components in guaranteeing the security and dependability of bonded structures in container building and construction - Tank Welding Inspection. These requirements serve to develop minimum demands for material buildings, welding procedures, and evaluation practices, therefore lowering the threat of architectural failures and enhancing total efficiency
Key companies, such as the American Culture of Mechanical Engineers (ASME) and the American Welding Culture (AWS), give standards that are extensively adopted in the sector. Conformity with these criteria not just guarantees adherence to finest methods yet likewise meets lawful and contractual obligations, safeguarding the rate of interests of stakeholders.
Regulatory bodies usually mandate adherence to details codes, such as ASME Code Area IX for welding certifications and API 650 for welded storage tanks. These codes describe requirements for welding strategies, certifications of personnel, and testing techniques to validate weld integrity.
Normal audits and evaluations are critical to preserving conformity, as they aid identify discrepancies from established requirements. Non-compliance can cause significant fines, task delays, and security risks. Therefore, a robust understanding of governing criteria and a dedication to conformity are critical in accomplishing top notch and long lasting welded container structures.
Non-Destructive Examining Methods
How can the integrity of welded pop over to these guys frameworks be guaranteed without creating damages? Non-destructive testing (NDT) techniques use a durable option, making it possible for assessors to evaluate weld high quality without compromising the material - Tank Welding Inspection. Amongst the most typical NDT methods are ultrasonic testing (UT), radiographic testing (RT), magnetic fragment testing (MT), and color penetrant testing (PT)
Ultrasonic screening utilizes high-frequency sound waves to identify internal problems and identify material buildings. It provides accurate measurements and is specifically efficient for thick materials. Radiographic testing includes passing X-rays or gamma rays through the weld, creating photos that expose structural issues such as fractures read the full info here or voids. This approach is indispensable for evaluating the honesty of complicated welds.
Magnetic fragment testing is matched for ferromagnetic materials, where electromagnetic fields disclose surface and near-surface suspensions. Color penetrant testing utilizes a fluid color to highlight surface-breaking defects, making it a reliable method for non-porous products.
Each of these NDT approaches has unique benefits, allowing for detailed evaluations tailored to specific materials and welding procedures. By executing these strategies, industries can ensure the dependability and safety and security of welded structures, inevitably boosting overall efficiency.
Enhancing Weld Top Quality With Assessment
Effective assessment plays a crucial function in enhancing weld high quality, offering as an essential checkpoint in the fabrication process. By determining possible flaws early, inspections reduce the risk of jeopardized architectural integrity and guarantee compliance with sector criteria. Using a mix of aesthetic examinations, non-destructive testing (NDT) methods, and mechanical about his assessments, inspectors can discover problems such as porosity, splits, and insufficient blend.
Applying a robust inspection protocol not just boosts the total top quality of welds yet additionally promotes a society of responsibility among welders and fabricators. Routine training and certification of inspection personnel guarantee that they are geared up with the necessary skills to recognize and address possible troubles successfully. This positive method minimizes rework and associated prices, eventually adding to predict effectiveness.
Moreover, extensive documentation of assessment findings provides beneficial understandings into recurring concerns, assisting in continuous renovation in welding methods. By leveraging innovative modern technologies, such as automated ultrasonic screening or digital radiography, weld quality can be boosted with a lot more specific evaluations. Finally, an extensive assessment procedure is essential in attaining top notch welds, guaranteeing safety and security, integrity, and durability in tank manufacture.
Final Thought
In verdict, the implementation of rigorous tank welding examination requirements and approaches is important for ensuring weld honesty and performance. By making use of a mix of visual examinations, non-destructive testing techniques, and adherence to regulative requirements, companies can properly determine and mitigate prospective defects.